Die Unternehmen Plasmatreat GmbH und Venjakob Maschinenbau GmbH & Co. KG haben in Ostwestfalen-Lippe eine Partnerschaft geschlossen, um eine innovative Lösung für die Batteriefertigung zu entwickeln. Durch den Einsatz eines neuartigen Verfahrens wird die Herstellung von Batteriezellen effizienter und zuverlässiger gestaltet. Statt einer aufwändigen Folienummantelung werden die Batteriezellen mit einer speziellen Plasma-reinigenden Beschichtung versehen. Dies bietet den Batterieherstellern eine Vielzahl von Vorteilen.
Inhaltsverzeichnis: Das erwartet Sie in diesem Artikel
Effizientere und zuverlässigere Batteriefertigung durch innovative Beschichtungstechnologie
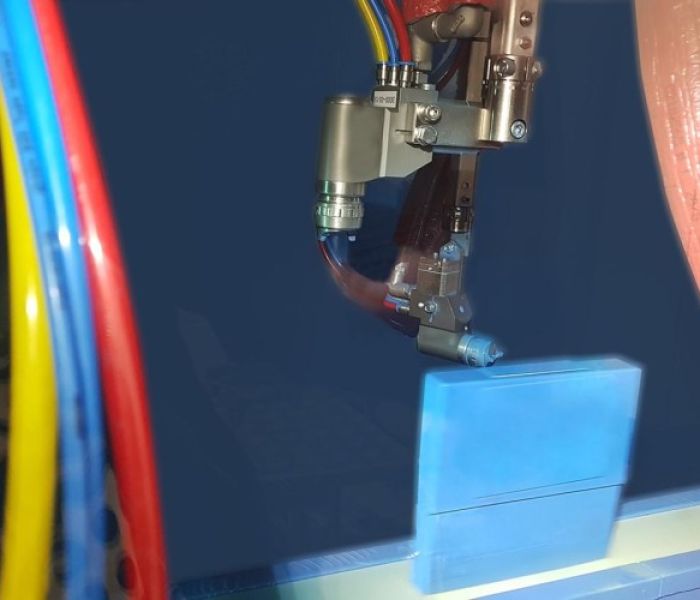
Blick in die Spritzlackierkabine der Batteriezellenbeschichtungslinie (Foto: Venjakob Maschinenbau GmbH & Co. KG)
Durch das Zusammenführen der Kompetenzen von Plasmatreat und Venjakob ist es gelungen, ein innovatives Verfahren zur Beschichtung von Batteriezellen zu entwickeln. Statt der herkömmlichen Folierung werden die Zellen nun mit einem speziellen Lack beschichtet, was zu einer effizienteren, schnelleren und zuverlässigeren Batteriefertigung führt. Dieser Prozess bietet zahlreiche Vorteile, da er kostengünstiger, zeitsparender und weniger fehleranfällig ist. Zudem verbessert er die elektrische Isolierung der Batteriezellen und trägt somit zur Steigerung der Zuverlässigkeit und Sicherheit im E-Mobility-Segment bei.
Weltmarktführer Plasmatreat entwickelt innovative Technologie für Batteriezellenreinigung und Lackauftrag
Die Openair-Plasma Technologie von Plasmatreat ermöglicht eine effektive und umweltschonende Reinigung von Batteriezellen. Durch den gezielten Einsatz von Druckluft und Strom werden hauchdünne Staubschichten, Öle und Fette zuverlässig entfernt. Dieser Prozess ist selektiv, effizient und kann direkt in der Produktion durchgeführt werden. Die Metalloberfläche der Batteriezellen wird dabei punktgenau gereinigt, um eine lückenlose Lackauftragung zu ermöglichen. Die Lackanhaftung ist langzeitbeständig, was die Zuverlässigkeit und Haltbarkeit der Batterien erhöht.
Effizientere Batteriefertigung durch berührungsloses Beschichtungsverfahren mit UV-Lack
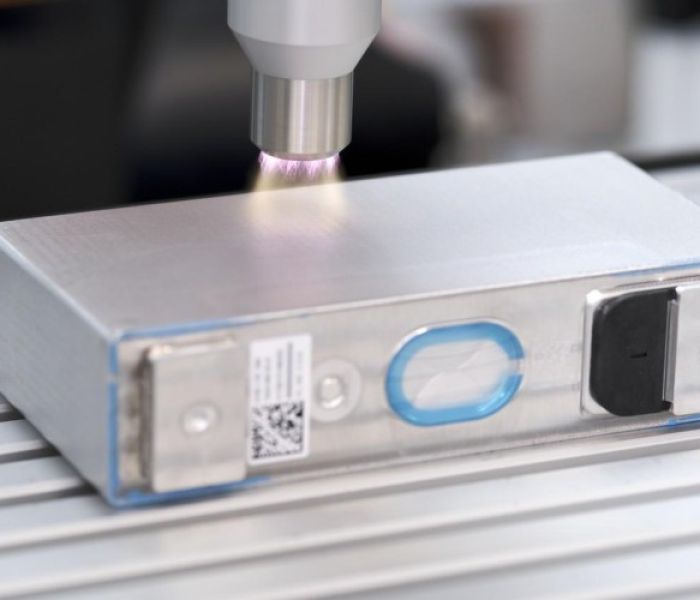
Durch Druckluft und Strom werden die Oberflächen der Batterien (Foto: THORSTEN ULONSKA, PLASMATREAT GmbH)
Venjakob, ein Maschinenbauunternehmen mit Expertise in Beschichtungslinien, hat eine vollautomatische Anlage für ein berührungsloses Beschichtungsverfahren entwickelt. Nach der Reinigung durch das Openair-Plasma werden Batteriezellen in verschiedenen Formaten mit einem 100-prozentigen UV-Lack überzogen. Dabei werden empfindliche Bereiche und die elektrischen Pole sicher vor Overspray geschützt. Der berührungslose Prozess minimiert das Risiko von Beschädigungen und ermöglicht eine erhöhte Produktionsgeschwindigkeit. Die sofortige Härtung des UV-Lacks ermöglicht eine direkte Weiterverarbeitung der Zellen und beschleunigt den gesamten Herstellungsprozess.
Hohe Wirksamkeit: Innovative Beschichtung verbessert Batteriehaftung in Zugschertests
Die Wirksamkeit der innovativen isolierenden Beschichtung wurde durch Analysen bestätigt. Mit Haftfestigkeitswerten von über 15 MPa in Zugschertests erfüllt sie hohe Anforderungen. Der Erfolg des Projekts basiert auf der optimalen Zusammenarbeit der Partner. Gemeinsames technologisches Know-how, hohe Qualitätsstandards, flexible Anpassungsfähigkeit an Kundenwünsche und eine intensive Kommunikation sind entscheidende Faktoren.
Dank der räumlichen Nähe von Plasmatreat und Venjakob können Kunden von der engen Zusammenarbeit der beiden Unternehmen profitieren. Die Feinstreinigung und Beschichtung der Batteriezellen können in den Werken in Steinhagen und Rheda-Wiedenbrück in einem seriennahen Prozess durchgeführt werden. Dadurch können die Prozesse optimal auf die individuellen Kundenanforderungen angepasst und die Ergebnisse direkt vor Ort evaluiert werden.
Effiziente und zuverlässige Batteriefertigung mit innovativer Beschichtungstechnologie
Durch die Zusammenarbeit von Plasmatreat und Venjakob wurde eine bahnbrechende Lösung für die Batteriefertigung entwickelt. Das innovative Verfahren ermöglicht eine effizientere und zuverlässigere Produktion von Batteriezellen durch den Einsatz einer speziellen Beschichtung anstelle einer komplexen Folienummantelung. Durch die enge räumliche Nähe der beiden Unternehmen können sie gemeinsam die Prozesse simulieren und Kleinserien herstellen, was den Kunden einen direkten Nutzen bietet. Diese wegweisende Lösung treibt das E-Mobility-Segment voran und führt zu einer erhöhten Zuverlässigkeit und Sicherheit von Batterien.